¡Hola, mecatrónicos!
Bienvenidos a una nueva entrega del blog de Sinadrives.
Febrero 2022
Hoy en esta nueva entrega hablaremos de la máquina herramienta y porque esta tiene tanta precisión.
Nota: Bajo el concepto “Máquina Herramienta” entendemos toda aquella maquinaria cuyo propósito es mecanizar piezas metálicas y no metálicas mediante el arranque de viruta. Hablamos de maquinaria como: tornos, fresadoras, rectificadoras, taladradoras, etc. La primera y posiblemente la más grande diferenciación de la máquina herramienta de todas las demás es la precisión de mecanizado, de rigidez y su gran robustez.
Seguramente el sector de la máquina herramienta es el más antiguo de todos los comprendidos dentro de la industria. Hubo un momento en la historia cuando hacía falta mecanizar el primer tornillo, la primera placa base y la primera polea para “la primera máquina”, en el que el sector tuvo que buscar soluciones artesanas para poder fabricar algunas piezas de alta precisión geométrica y garantizar las tolerancias de planitud, paralelismo o concentricidad. Todo aquello ya es pasado y en el día de hoy tenemos a nuestra disposición un extenso abanico de maquinaria herramienta para satisfacer las exigencias más altas, en cuanto a tolerancias geométricas y la precisión de las mismas.
¿Qué es la realimentación directa de posición?
La máquina herramienta debe gran parte de su éxito a la “Realimentación directa de posición”. Este método desde siempre ha sido aplicado en la máquina herramienta. La ventaja de este método consiste en medir la posición directa del carro (5) mediante un segundo encoder (8) y no, como es habitual, mediante el encoder (7) del servomotor (1). En el esquema adjunto se puede ver el principio de realimentación de posición directa.
1. Servomotor
2. Acoplamiento
3. Husillo de bolas
4. Tuerca del husillo
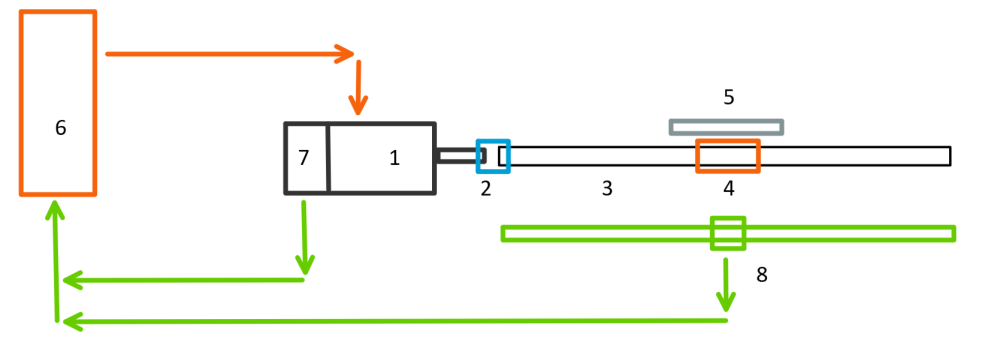
5. Carro móvil
6. Servo-accionamiento / CNC
7. Encoder del servomotor
8. Regla y encoder lineal
Ambos encoders (7) y (8) están conectados al servo-accionamiento / CNC (6). El encoder del servomotor (7) sirve como la referencia de velocidad, por eso puede ser de poca precisión, tipo resolver, mientras que el segundo encoder (8) (por norma suele ser una regla lineal óptica) sirve como la referencia de posición. De la precisión y la repetitividad de este encoder depende la precisión de posicionamiento de la máquina.
Ventajas de la realimentación directa
Este tipo de realimentación con un encoder directo mejora notablemente el comportamiento del eje, mejora la precisión y la repetitividad, aumenta la respuesta dinámica, disminuye la influencia de dilatación térmica, ignora por completo el error del paso mecánico de husillo (3, 4) y otros elementos mecánicos (2) de todo el conjunto.

Imagen 1. Fuente: Renishaw.
Falta destacar que el método de realimentación directa también se usa en las aplicaciones de motor lineal, motor torque o los módulos lineales con motor lineal. Este simple método mejora notablemente el comportamiento de cualquier máquina, sobre todo si es dinámica y la precisión requerida es alta.
¿Qué grado de precisión logra la realimentación directa?
Gracias a solución de realimentación directa los módulos con motor lineal alcanzan fácilmente precisión absoluta de hasta ± 3 micrómetros y una repetitividad de +- 100 nanómetros.
Claves para garantizar que la máquina herramienta sea precisa
1. Componentes mecanizados de máquina herramienta.
Aquí hablamos de componentes como la base, la mesa, el carro móvil y los raíles. Los componentes de una máquina herramienta son la clave para garantizar la precisión requerida. La manera más fácil de conseguir un conjunto de precisión es tener piezas de alta calidad que cumplen con las tolerancias indicadas y tienen características de precisión geométrica dentro de los márgenes establecidos. La calidad de los acabados y la precisión geométrica de estos componentes es la clave.
2. Componentes estándares
Hablamos de los componentes estándares como: rodamientos, guías, CNC, accionamientos, motores torques, encoders, etc. A día de hoy existe una amplia oferta de componentes específicos para este mercado para garantizar los requerimientos más exigentes de precisión.
Estos componentes ya cumplen con la mayoría de exigencias y requerimientos para realizar aplicaciones de máquina herramienta, tales como precisión, repetitividad, potencia, software, algoritmos específicos, tablas de compensaciones, etc.
3. Montaje y ajuste
El montaje y el ajuste de una máquina herramienta es todo un capítulo aparte. Existe un dicho que dice: “Aun que tengas todos los planos de las piezas y las tengas mecanizadas según las tolerancias exigidas, sin la experiencia adecuada, no serás capaz de montar una máquina que funcione correctamente.”
En las empresas que fabrican máquinas herramienta, los ajustadores tienen un estatus especial y se consideran como empleados clave de la organización.
4. Calibración
Una vez la máquina montada siempre viene la fase de calibración. Se calibran los ejes lineales y rotativos según la precisión absoluta y se corrigen errores de medición de los encoders y sensores de posición.
4.1 Calibración láser
Este tipo de calibración se utiliza para reducir el error de precisión absoluta mediante calibración láser. El carro móvil se lleva a la posición 100 mediante el encoder y este valor de posición se compara con la medición del láser. La diferencia entre ambas posiciones se introduce en la tabla de corrección de control numérico.

Imagen 2. Fuente: Renishaw.
4.2 Calibración Ballbar
Este tipo de calibración permite ajustar perpendicularidad de ejes. La prueba consiste en realizar un movimiento circular y compararlo con la medición de la Ballbar.

Imagen 3. Fuente: Renishaw.
Tendencias y novedades del sector
Motores lineales y motores torques
Una de las principales tendencias del sector es la integración de accionamientos direct drive en las aplicaciones de máquina herramienta. El motor directo (o un motor toque) rotativo ya es un componente habitual en las fresadoras o los tornos. En cuanto a motor lineal, la aplicación de este tipo de accionamiento cada vez es más utilizada en aplicaciones de alta dinámica y precisión.
Encoders
Otro componente muy solicitado son los encoders lineales y rotativos robustos, de tecnología inductiva. Estos tipos de encoders permiten un funcionamiento seguro bajo condiciones ambientales muy complicadas como puede ser viruta, humedad o taladrina.
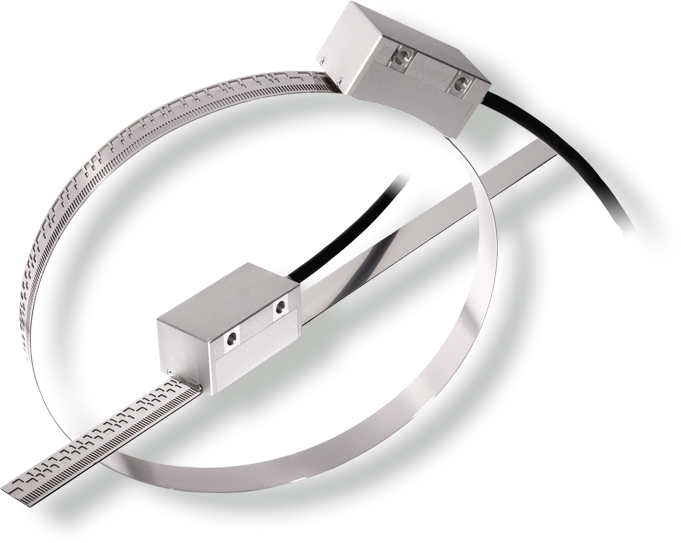
Imagen 4. Fuente: Heidenhain.
Usted también puede aprovechar las ventajas y la experiencia de la máquina herramienta. Si tiene una aplicación donde necesita mejorar la dinámica, la precisión o repetitividad estaremos encantados de ayudarle. Aproveche la experiencia de más de 15 años en el mercado de maquinaria y automatización.
Si tienes una aplicación donde te interesa mejorar las prestaciones de tu máquina ya sea velocidad, dinámica, precisión o simplemente reducir su mantenimiento ponte en contacto con nosotros.
Nuestros especialistas en tecnología Direct Drive y Módulos lineales con motor lineal te asesorarán de manera gratuita.
¡Hasta la próxima!
El equipo Sinadrives.
Get Social