Hallo Mechatroniker!
Willkommen zu einer neuen Ausgabe des SINADRIVES-Blogs mit dem Thema: Linearmotorantrieb vs. Pneumatikzylinder
August 2020
Ob als Praktikant, Auszubildender oder Student und uns wurde immer gesagt: Wenn man etwas auf einfache Weise bewegen will: Ein Pneumatikzylinder Ventil und schon ist die Anwendung einsatzbereit. Wirtschaftlich, einfach und wartungsfreundlich. Diese Auffassung ist bis heute so geblieben und Pneumatikzylinder sind so die beliebtesten und in der Industrie am weitesten verbreitet.
Klar um von Punkt A nach Punkt B zu gelangen ist es einfach. Was aber wenn die Anwendungen eine bestimmte Geschwindigkeits-, Kraft- oder Positionsregelung erfordern? Solche Anwendungen mit einem Pneumatikzylinder zu lösen, ist nicht mehr so einfach. Jetzt kommen elektromechanische Antriebe ins Spiel. Unter dem Begriff elektromechanischer Antrieb verstehen wir Linearmotor-, Spindel-, Zahnriemen- und Zahnstangenantriebe.
Art der Anwendungen und wo ein elektromechanischer Antrieb erforderlich ist.
Es gibt eine Vielzahl von Anwendungen, bei denen die Steuerung von Geschwindigkeit, Beschleunigung, Drehmoment, Kraft oder Position erforderlich sind um bestimmte Prozesse durchzuführen. Als Beispiel können wir einige der folgenden Aufgaben auswählen:
1. Bewegung mit variabler Geschwindigkeit.
Die Geschwindigkeit variiert ständig und passt sich dem Bedarf des Prozesses an. Anwendungsbeispiele: Pressenbeschickung, fliegendes Zuschneiden, Synchronisationswellen, elektrische Kurvenscheiben, Pressen usw. In Bild 1 zeigen wir Geschwindigkeitskurven einer fliegenden Zuschneidanwendung.
Bild 1
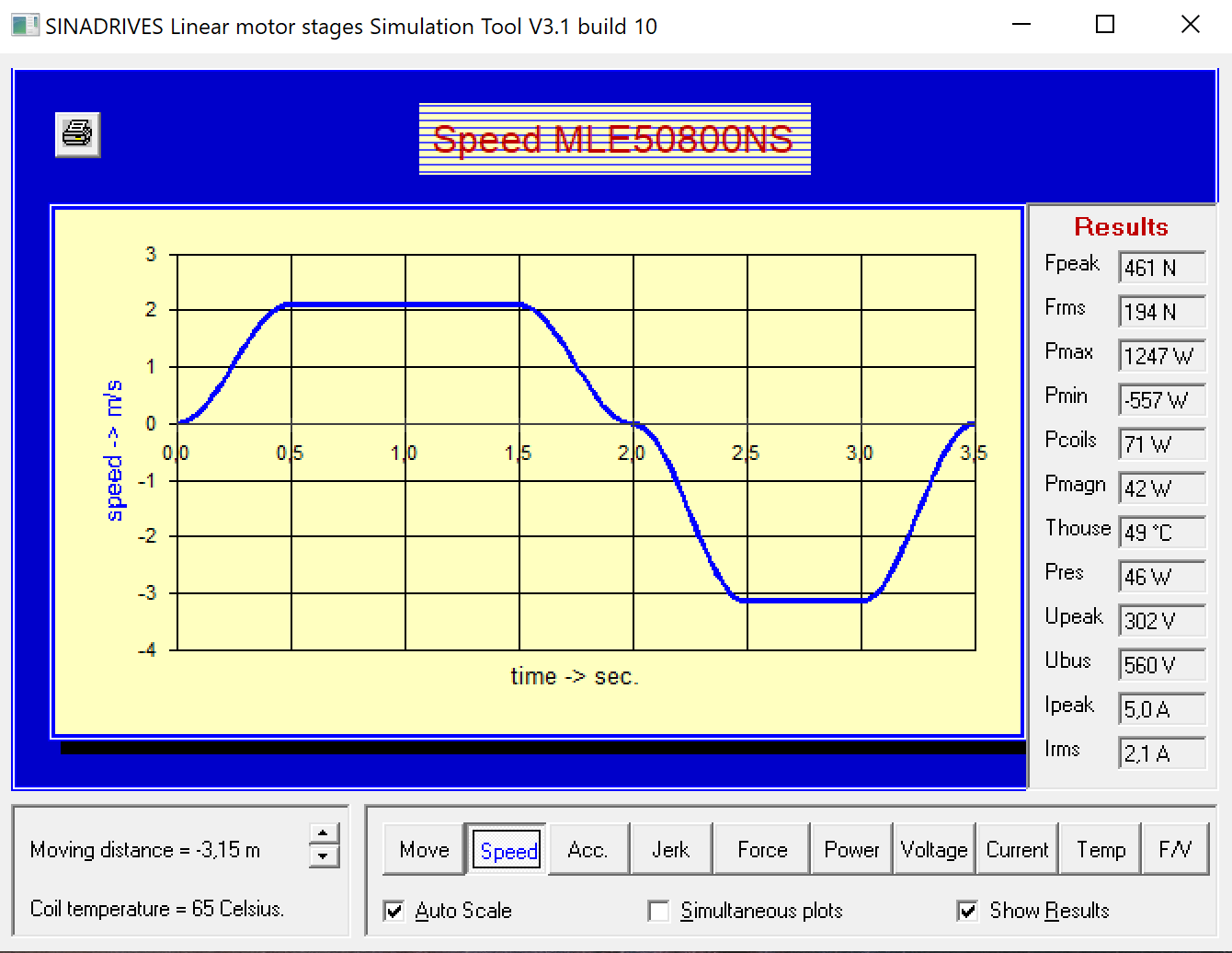
Bei dieser Art von Anwendung ist ein elektromechanischer Antrieb die einzige Lösung. Nur ein Antrieb dieser Art kann die exakte Erfüllung der Positionstabelle gewährleisten. Wenn wir hinzufügen, dass der Antrieb über einen Linearmotor erfolgt, verbessern wir Positionierparameter wie Dynamik, Präzision und können vor allem „Rebounds“ und Schleppfehler reduzieren.
2. Bewegung mit variabler Geschwindigkeit, Beschleunigung und Ruck.
Geregelt wird nicht nur die Geschwindigkeit, sondern auch Beschleunigung und/oder Ruck. Diese Art der Steuerung hilft, Vibrationen und Resonanzen zu vermeiden und Spurfehler zu reduzieren. Es ist beliebt bei Anwendungen, bei denen eine präzise Bahnsteuerung erforderlich ist. Anwendungsbeispiele: Laserschneiden, ultraschnelle Positionierer usw. In den Bildern 2 und 3 zeigen wir Beschleunigungskurven und Ruckkurven einer Positionieranwendung.
Bild 2

Bild 3

Bei dieser Art von Anwendung ist die Regelkreisgeschwindigkeit alles. Linearmotorantriebe bieten die besten Zeiten für die Schleifensteuerung. Dank eines direkt im Fahrwagen integrierten Encoders werden Dynamik und Lageregelung sehr präzise.
3. Bewegung mit konstanter Geschwindigkeit.
Bei manchen Prozessen wird auf konstante Geschwindigkeit Wert gelegt. Geschwindigkeitsfehler können sehr kritisch sein. Wir wissen, dass aufgrund des PID-Regelkreises immer ein Fehler auftritt, aber bei solchen Anwendungen muss der Fehler minimiert werden. Anwendungsbeispiele: Lasergravur, Digitaldruck etc.
In Bild 4 zeigen wir eine Positionierung mit einer Geschwindigkeit von 16 Mikrometer / Sekunde, in Lila zeigen wir die Position in Mikrometer und in Grün den Geschwindigkeitswert in Mikrometer / Sekunde und die X-Achse ist die Zeit in Sekunden.
Bild 4

Linearmotortechnologie kombiniert mit einem hochauflösenden Encoder und hoher absoluter Präzision sorgt für minimalen Geschwindigkeits-Jitter. Zudem erleichtert das Fehlen von Getrieben die Kontrolle und vermeidet Überraschungen
4. Bewegung mit Kraftkontrolle
Bewegungs- und Kraft- (oder Drehmoment-)Steuerung hängen von dem geforderten Prozess ab. Der elektromechanische Antrieb bietet eine exakte Kontrolle dieses Parameters. Anwendungsbeispiele: Servopressen, Nieten, Einfädeln, Stanzen, Siebdruck etc.
Diese Anwendungen erfordern eine sehr genaue Kraftsteuerung. Der andere Name für Linearmotoren ist Direct Drive. Direkt bedeutet, dass es durch die direkte Kopplung an den Schlitten sofort Kraft- und Stromverbrauchsänderungen erkennt. Das Fehlen von Übertragungswerten spart wertvolle Millisekunden und korrigiert die Kraftanwendung sofort.
5. Bewegung mit Positionskontrolle
Es geht nicht nur darum, von Punkt A nach Punkt B zu gehen, es braucht auch Zwischenstopps mit einiger Genauigkeit und Präzision. Anwendungsbeispiele: Palettierer, Cutter, 3D-Drucker, etc.
Es geht nicht nur darum, die Achse an den angegebenen Punkten zu positionieren. Wir können eine Positionierung mit hoher Präzision und Wiederholgenauigkeit garantieren. Auf Kundenwunsch ergänzen wir die Messergebnisse und die notwendigen Prüfungen.
In Bild 5 zeigen wir ein Beispiel für eine Achsverifikation mit einem Laser Interferometer. Die absolute Genauigkeit des Encoders und die absolute Genauigkeit der mechanischen Teile werden überprüft.
Bild 5

Das sind einige Beispiele von Anwendungen bei denen ein Einsatz von elektromechanischen Antrieben erforderlich ist. Dabei ist zu beachten, dass die Herausforderungen, denen wir uns in diesem Bereich stellen müssen, täglich größer werden. Neben der reinen Fokussierung auf Positionieraufgaben bietet ein elektromechanischer Antrieb viele weitere Vorteile. Einige davon haben wir im nach folgend zusammengefasst.
Vorteile elektromechanischer Antriebe:
Frei programmierbar
Einer der Vorteile eines elektromechanischen Antriebs, egal ob Linearmotor, Zahnriemen oder Spindel, ist die Möglichkeit der freien Programmierung. Da die Antriebssteuerung über eine Positioniereinheit (SPS oder CNC) erfolgt, können beliebig viele Programme geladen werden. Auf diese Weise kann die Maschine für ein anderes Teil oder einen anderen Prozess umprogrammiert oder Anpassungen und Modifikationen vorgenommen werden, die zur Anpassung/ Verbesserung des Prozesses nötig sein können. So können Abläufe, Geschwindigkeit, Beschleunigung usw. nach Belieben geändert werden.
Verfügbarkeit über alle Daten des Prozessablaufs
Dank der exakten Ansteuerung eines elektromechanischen Antriebs ermöglichen moderne Steuerungen (SPS und CNC) und Servoantriebe die sehr genaue Erfassung bestimmter Parameter. Über Oszilloskopfunktionen können Parameter wie Geschwindigkeit, Beschleunigung, Positionsfehler, Schleppfehler, Stromaufnahme, Antriebstemperatur etc. angezeigt werden. Vergessen wir nicht, dass all dies in Echtzeit mit einer Genauigkeit von einer Millisekunde. Wir können Trigger aktivieren, visualisieren und digitale Ein-/Ausgänge überwachen, alles mit dem Ziel, unseren Prozess zu verbessern.
Integrierte Oszilloskopdaten helfen uns, Probleme zu lösen, die mit dem menschlichen Auge oder auf den ersten Blick nicht erkennbar waren. Der Detaillierungsgrad und die Präzision dieser Werkzeuge sind so tiefgreifend, dass sie dem Instandhaltungsleiter oder Inbetriebnahmetechniker ihre Arbeit erleichtern.
Industrie 4.0 und vorbeugende Instandhaltung
Diese Informationen, die bereits digitalisiert und auf einfache Weise aus den SPS und CNC Steuerungen extrahiert werden können, machen es uns möglich eine schnelle Steuerungs- und Optimierungsprotokolle anzuwenden. Industrie 4.0 ist nur möglich mit dem Einsatz von Daten und hier haben erhalten wir sie.
Als Beispiel können wir den Fall der Temperaturregelung anführen. SINADRIVES Linearmodule verfügen über 2 Temperatursensoren: PTC und KTY. Der PTC Sensor ist ein reiner Kontakt, der sich ab einer bestimmten Temperatur im Inneren des Linearmotors öffnet. Der KTY Sensor gibt zu jedem Temperaturwert einen Widerstandswert an. Das heißt, wir können die Laufwerkstemperatur in Echtzeit überwachen. Wenn wir die Möglichkeit hinzufügen, sie mit der Umgebungstemperatur (oder der Temperatur des Schaltschranks) zu vergleichen, können wir diese beiden Werte analysieren und überwachen, ob sich der Unterschied zwischen beiden ändert. Wenn wir feststellen, dass die Temperatur des Linearmotors 5 °C oder mehr über dem Normalwert liegt, können wir den Techniker präventiv vor einem möglichen Verschleiß oder einem zukünftigen Problem warnen.
Energieverbrauchskosten
Wir werden uns nicht verabschieden, ohne das Thema Energieverbrauch an zu sprechen. Die Anschaffungskosten für einen Pneumatikzylinder sind im Vergleich mit einem elektromechanischen Antrieb sehr gering. Wir können von einem Verhältnis von 4:1 bis 10:1 sprechen. Der elektromechanische Aktuator kostet 4-10 mal mehr. Im allgemeinen kann man davon ausgehen das ein Pneumatikzylinder nach 12-15 Monaten Einsatz aufgrund des Wirkungsgrades der Kompressoren, Verluste in den Druckluftleitungen und der Wartungskosten der Druckluftsysteme teurer zu werden als ein elektromechanischer. Auch wenn wir einen elektromechanischen Antrieb nur für das Positionieren von Punkt A nach Punkt B einsetzen, ohne die anderen erläuterten Vorteile zu nutzen ist ein Pneumatikzylinder auf Dauer teurer.
Ziehen Sie Ihre eigenen Schlüsse. Entscheiden Sie welchen technischen Stand Sie Ihrer Maschine geben wollen um wettbewerbsfähig zu sein. Wir können Ihnen dabei helfen.
Wenn Sie weitere Informationen zu dem Thema Linearmotorantrieb (elektromechanisch) gegen Pneumatikzylinder wünschen, können Sie unsere Website (www.sinadrives.com) besuchen oder uns über einen Kommentar in diesem Blog kontaktieren.
Gerne stehen wir Ihnen auch telefonisch und persönlich zu diesem und allen anderen Themen zur Verfügung.
Wir sehen uns in der nächsten Ausgabe. Bis dahin alles Gute!
Ihr SINADRIVES Team.
Get Social