Hello Mechatronics,
August 2021
As students and trainees we were always told: “If you need to move something in a simple way, use a pneumatic cylinder, because with only 2 pins, a little compressed air, a solenoid valve and determining the stroke length, the application is ready. Economical, simple and easy to maintain. Today this remains just as simple, with compressed air drives being the most popular and most widely used by industry. Getting from point A to point B is easy, but what if the applications demand a certain level of speed, force or position control? Providing solutions for these types of applications requiring a pneumatic cylinder is no longer so simple. This is when electromechanical drives come into play. The concept of an electromechanical drive refers to a linear motor, spindle, toothed belt and rack drives.
Type of applications and when a linear motor with electromechanical drive is required
There are a multitude of applications where the control of speed, acceleration, torque, force or position can be decisive when carrying out certain processes. For example, some of the following tasks:
1. Variable speed movement
The speed varies at all times, adjusting to process requirements. In applications such as: press feeding, flying cutting, synchronization shafts, electric cams, presses, etc. Image 1 shows the speed curves of a flying cutting application.
Image 1
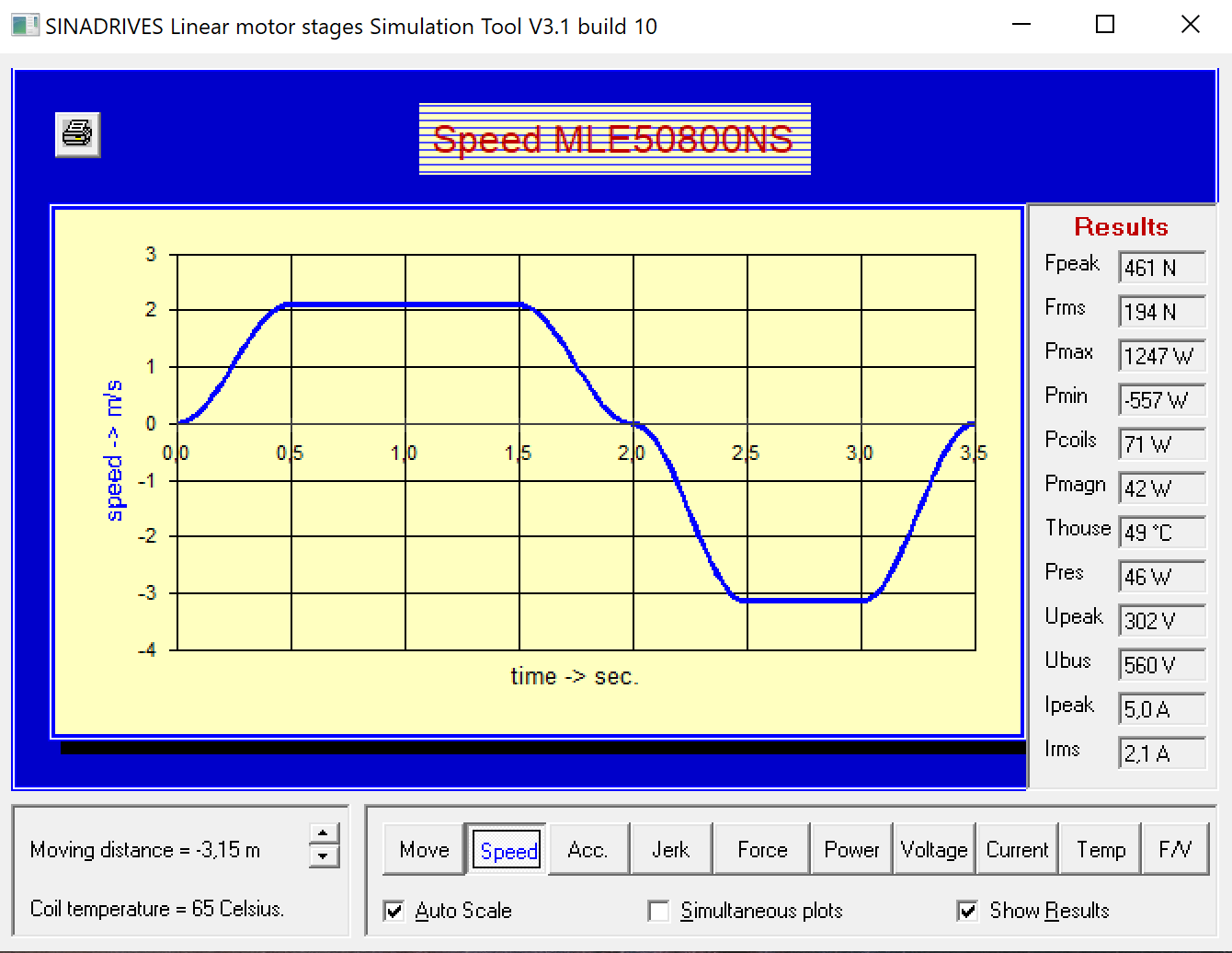
In this type of application, an electromechanical drive is the only solution. Only a drive of this type can guarantee the fulfilment of the position table with a high degree of accuracy. Likewise, a linear motor drive, improves positioning parameters such as dynamics, precision and above all “rebounds” and tracking errors can be reduced
2. Movement with variable speed, acceleration and jerk
Not only is speed controlled, but also acceleration and / or jerk. This type of control helps prevent vibrations, resonances and reduces tracking error. It is popular in applications where precise control of the axis path is required. In applications such as: Laser cutting, ultra-fast positioners. Images 2 and 3 show the acceleration curves and Jerk curves of a positioning application.
Image 2

Bild 3

In this type of application, control loop speed is everything. Linear motor drives offer the best times for loop control. Thanks to an encoder integrated directly in the mobile carriage, the dynamic response and position control become very precise.
3. Movement with constant speed
In some processes constant speed is valued and speed errors can be very critical. Errors are always present due to the PID control loop, but in certain types of applications the error has to be minimized. In applications such as: laser engraving, digital printing, etc. Image 4 shows positioning at a speed of 16 micrometres / second, the position in micrometres is shown in purple and the speed value in micrometres / second in green, the X axis is time in seconds.
Image 4

Linear motor technology combined with a high resolution encoder and high absolute precision ensures minimal speed jitter. In addition, the absence of transmissions facilitates control and avoids any surprises.
4. Movement with torque control
Movement and torque (or force) control depend on the required process. The electromechanical drive offers exact control of this parameter. In applications such as: Servo presses, riveting, threading, stamping, pad printing, etc. These types of applications require very precise force control. The other name for linear motor is Direct Drive. Direct means that by being directly coupled to the mobile car, it immediately detects changes in force and current consumption. Having no transmissions saves valuable milliseconds and corrects workforce.
5. Movement with position control
It is not only about going from point A to point B, intermediate stops with some degree of accuracy and precision are also required. In applications such as: Palletizer, cutters, 3D printer, etc. It is not only a matter of positioning the axis at the indicated points, positioning can also be guaranteed with great precision and repeatability. The results of measurements and the necessary checks can be added if required by the customer. Image 5 shows an example of an axis verification using a laser interferometer. The absolute precision of the encoder and the absolute precision of the mechanical part are verified.
Image 5

These were just some of the examples of applications that require an electromechanical drive. It should be noted that we are faced with increasing challenges in this field on a daily basis. In addition to focusing purely on positioning tasks, there are numerous other benefits an electromechanical drive can offer, some of which include:
Advantages of linear motor elechtromecanical drives
Free programming
One of the advantages of an electromechanical drive, whether it is driven by a linear motor, toothed belt or spindle, is the possibility of reprogramming. As the drive control is through a Positioner (PLC or CNC), there is no limit to the programs. In this way, the machine can be reprogrammed to a different part or process, making any adjustments and modifications necessary to improve the process. Routes, speed, acceleration, etc., can be modified to suit your needs.
Accurate process information
Thanks to the exact control of an electromechanical drive, modern controls (PLCs and CNCs) and servo drives allow very exact captures of specific parameters. Using oscilloscope functions, parameters such as speed, acceleration, position error, tracking error, current consumption, drive temperature, etc. can be displayed. Let’s not forget that all of this is in real time with a precision of one millisecond. We can activate and view triggers, monitor digital inputs / outputs, all with the aim of fine-tuning our process as much as possible. Integrated oscilloscope data help solve problems undetected by the human eye. The level of detail and precision of these tools is so profound that undoubtedly it makes the life of the maintenance manager or commissioning technician easier.
Industrie 4.0 and preventive maintenance
All this information within our reach is also already digitized and can be extracted in a simple way from the PLCs and CNCs, enabling the necessary control and optimization protocols to be implemented. Industry 4.0 needs data which we have at our fingertips. One example is the case of temperature control. SINADRIVES linear modules have 2 temperature sensors: PTC and KTY. While PTC is purely a contact that opens from a certain temperature inside the linear motor, KTY is a sensor that emits a resistance value for each temperature value. I.e., the drive temperature can be monitored in real time. If we add the possibility of comparing it with the ambient temperature (or the temperature of the electrical cabinet) we can analyse these two values and monitor if the difference between them changes. If we observe that the temperature of the linear motor is 5ºC above normal, we can preventively warn the technician about possible wear or a future problem.
Energy consumption costs
We couldn’t sign off without mentioning the issue of energy consumption. The costs of a pneumatic cylinder are very low; we are talking about a ratio from 4:1 to 10:1 if we compare it to an electromechanical actuator (an electromechanical actuator costs 4-10 times more than a pneumatic cylinder). As a rule of thumb, after 12-15 months of use, a pneumatic cylinder starts to be more expensive than an electromechanical one due to the low efficiency of the compressors, large losses in the air circuits and the maintenance costs of compressed air systems. Even if the electromechanical drive is only used as a positioner at points A and B, without making use of all the other advantages explained in this article, a pneumatic cylinder is more expensive in the long run.
Draw your own conclusions. Decide which innovation you want to implement in your machine to be competitive. We can help you.
Your SINADRIVES Team,
Get Social